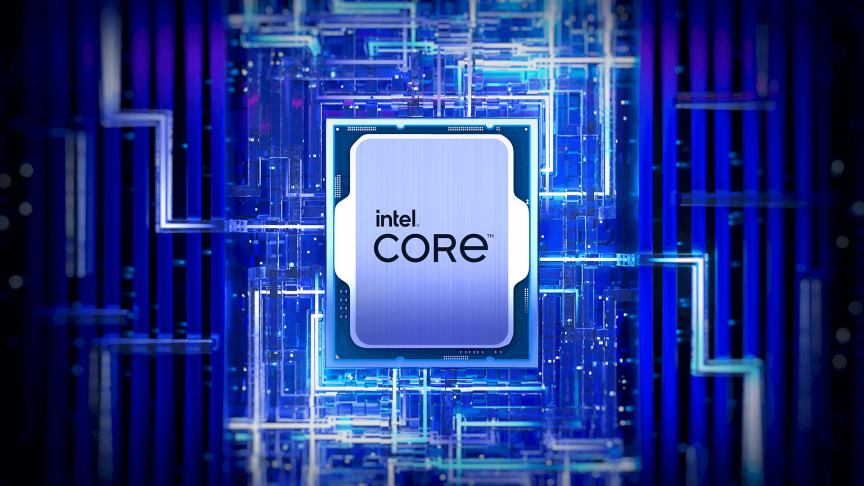
Intel recently revealed that its upcoming Core Ultra chip, Lunar Lake, won’t be produced in-house, and now the same applies to its next-generation desktop chip, Arrow Lake. While this shift to working with “external partners” for manufacturing is notable, it’s unlikely to impact the chip’s release schedule, features, or performance, including clock speeds. However, relying on outside factories like TSMC may increase production costs, potentially affecting consumer pricing.
For Intel, this decision marks a break in tradition. The company has prided itself on manufacturing its own chips for decades, but CEO Pat Gelsinger confirmed that high-profile chiplets like Lunar Lake and now Arrow Lake will be produced externally. This shift in strategy is both practical and symbolic.
The reaction to Intel’s decision can go two ways. On one hand, Intel views this as a positive development. Originally, Arrow Lake was supposed to be built using Intel’s 20A process, part of the company’s ambitious “five nodes in four years” plan. But Intel is now moving even faster, skipping 20A and moving straight to 18A, which they see as a sign of success: “One of the benefits of our early success on Intel 18A is that it enables us to shift engineering resources earlier than expected.”
However, this move could also be interpreted as a negative. Despite massive investments in its Intel Foundry business and additional funding from the U.S. government, Intel still hasn’t secured any major external customers for its foundry services. Add to that recent layoffs and cost-cutting efforts, and some might see the reliance on external manufacturing for Arrow Lake as a sign of weakness rather than progress.
Intel’s focus now shifts to its 18A process, set to debut with the Panther Lake chip in 2025. While defect density in the 18A process is promising, the use of an external foundry for Arrow Lake raises questions about Intel’s long-term manufacturing capabilities.